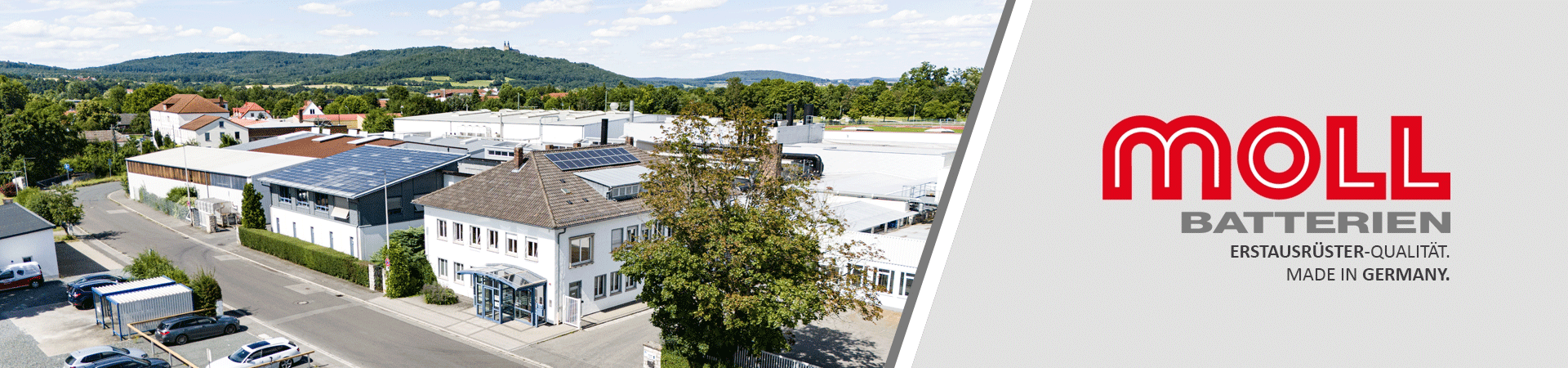
Pioneering Work for Europe
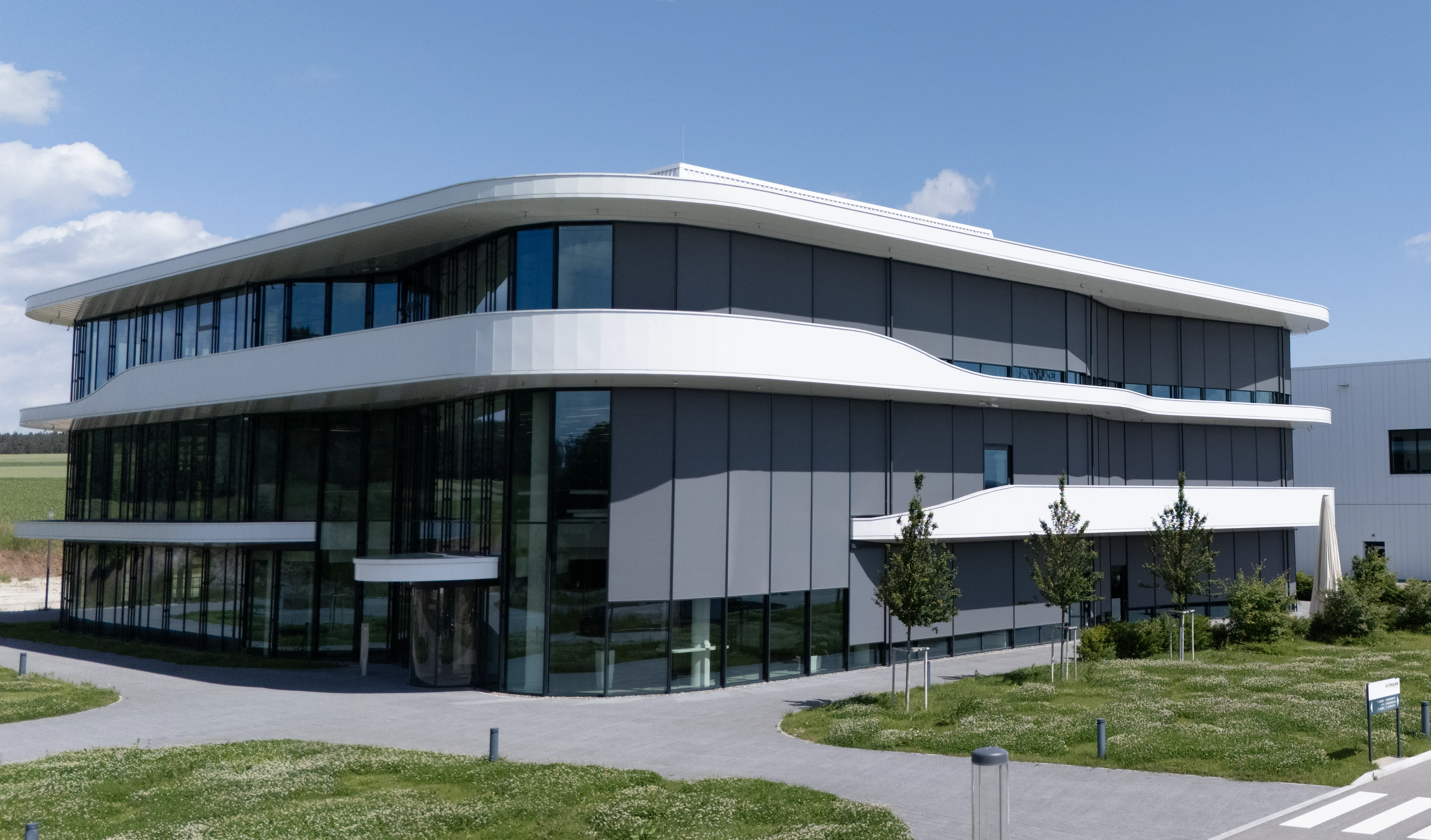
Bad Staffelstein/Lichtenfels – Lichtenfels will be the first location in Europe in 2025 where sodium-ion batteries will be produced. The company Moll is investing 80 million euros in Schney to build up industrial production with a capacity of one GWh. Initially, 120 jobs will be created. If everything goes according to plan, the workforce could later grow by another 500 people. It is also a first step towards becoming independent from Asian suppliers. Currently, they dominate particularly in the field of lithium-ion batteries.
Reducing Dependence on Asia
"For us, this is the opportunity to be part of the ramp-up of a new battery technology. We don't know of any other manufacturer in Europe that has such plans," says Peter Urban from Moll's management. The battery manufacturer, with its main plant in Bad Staffelstein, currently produces around 1.4 million conventional lead batteries primarily for cars and employs 230 people. Customers are manufacturers, especially the VW Group. They also supply the spare parts market. Production is currently running at full capacity, with batteries practically rolling directly onto the truck pallets.
Further Investments in the Main Plant
But is this the future? At Moll, the answer can be both yes and no. Lead batteries for cars will still be needed for decades, and Moll is also continuously developing this technology. One focus is on batteries for hot countries. The climate conditions are particularly hard on batteries here. "This leads to significantly shortened service life. Moll already has corresponding products in its portfolio," says Klaus Eichhorn from Moll's management. Recently, a development contract from the automotive industry was added to make further progress in this area. Additionally, investments continue at the Bad Staffelstein plant. Currently, an automatic pocketing machine for the lead plates is being ramped up, which will enable a significant production increase on the existing space. Around 2.6 million euros were invested in this alone.
The factory in Schney, however, opens a completely new chapter for the company: It will not only be a different technology but initially also target entirely different customer groups.
An important application will be decentralized buffer storage systems in container construction, which store excess energy from wind power, solar cells, and hydropower. When needed, they feed the electricity back into the grid locally, eliminating the need for transport over longer lines. At the same time, they help stabilize the power grid overall.
Quickly Catching Up
Asian competitors still have a head start. The car manufacturer BYD, for example, already presented a small car with sodium-ion batteries in mid-2023. Alternatively, more expensive lithium iron phosphate batteries are used, which have a higher energy density. However, even this battery type has lower storage capacity than the even more expensive lithium-ion batteries currently used in electric cars in Europe. The cheaper batteries are only an option for small vehicles with limited range.
Peter Urban currently doesn't see the main application of sodium-ion batteries in automotive manufacturing: "However, the energy density will certainly increase through further development."
The Asians' manufacturing lead doesn't worry him: "I think of companies like Toyota. They didn't start car production first either, but today they are the world's number one manufacturer and build very good vehicles."
Hofmann Plant Being Acquired
Three factors make Moll optimistic: In Schney, Moll has access to a modern, vacant plant with 10,000 square meters of production space and 5,500 square meters of office space. The company Werkzeugbau Hofmann had only built it in 2019 and inaugurated it in 2021. The plans dated from before the Corona crisis. But changes in the automotive industry, among others, have thwarted the company's plans. At the end of January, Hofmann announced that 50 of the 330 employees would have to be laid off and production would be completely relocated back to the main plant just a few hundred meters away. This was the only way to cope with the decline in sales. Shortly before, in November, the first contact between Hofmann and Moll was established. "We quickly reached an agreement," says Urban. Currently, there are also talks about taking over employees who lost their jobs at Hofmann.
The second point is production: "In principle, the technology is proven," says Urban. The machines are similarly constructed to those used in lithium-ion production. "The big difference is the chemistry, particularly that sodium is processed instead of lithium," says Klaus Eichhorn.
Raw Materials Readily Available
The third point concerns raw materials, prices, and further development: Sodium is available in Germany in large quantities and at low cost, for example in the form of sodium chloride, or table salt. Lithium is rare and is partly mined under ethically questionable conditions. Already now, the production costs for sodium-ion batteries are up to 40 percent lower than for lithium batteries, and they are more easily recyclable. Additionally, the fire hazard is significantly lower.
Moll is in contact with the University of Erlangen and the Bavarian Center for Battery Technology at the University of Bayreuth regarding cooperation in research and development. The buildings in Schney offer many options with their generous spaces.
Expansion Possibilities in Schney
When production in Schney slowly ramps up around mid-2025, they are aiming for an annual capacity of one GWh. By 2026/27, capacity could increase to five GWh. This would still make them a small player globally, says Urban.
But there are expansion areas in Schney – and above all, this technology will no longer be left solely to Asian competitors.